Comprendre et maîtriser les enjeux du Lean Manufacturing
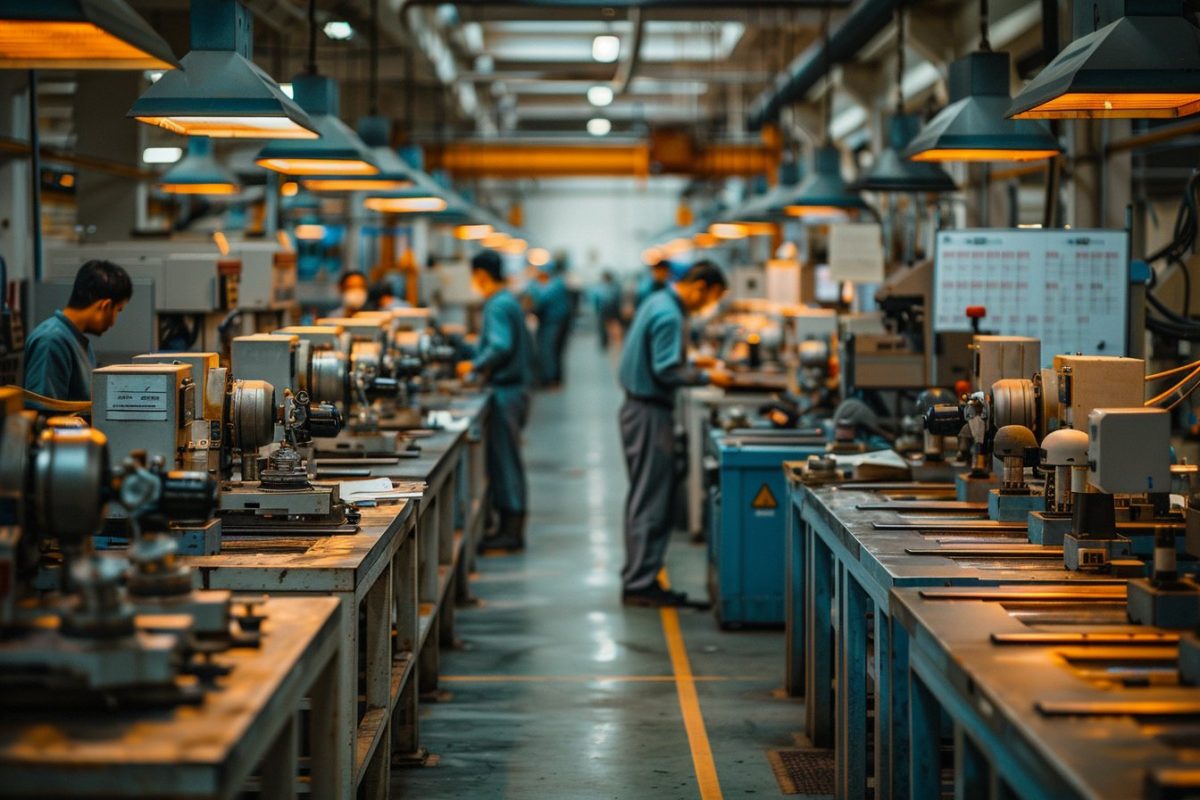
Le Lean Manufacturing, ou production allégée, est une méthode de management qui vise à améliorer la performance des entreprises en réduisant les gaspillages et en optimisant l’efficacité des processus industriels. En se concentrant sur l’augmentation de la productivité et la qualité tout en minimisant les coûts, cette approche s’est rapidement imposée comme un référentiel incontournable pour nombre d’entreprises cherchant à rester compétitives. Dans cet article, nous explorerons les principales concepts et techniques éprouvées de cette méthode.
Les principes fondamentaux du Lean Manufacturing
Le Lean repose sur cinq principes essentiels qui guident les entreprises dans la mise en œuvre de leurs actions d’amélioration continue :
- Valeur perçue par le client : Il s’agit de comprendre et de répondre aux attentes du client, contribuant ainsi à la satisfaction de celui-ci et au succès de l’entreprise.
- Cartographie de la chaîne de valeur : Cet outil consiste à identifier, analyser et éliminer les étapes non ajoutant pas de valeur aux produits et services fournis.
- Flux continu : Il désigne l’enchaînement sans interruption des différentes opérations de production, permettant de réduire les délais et les coûts associés.
- Tirer plutôt que pousser : Ce principe suggère de ne produire que ce qui est demandé par le client et en fonction du réel besoin, évitant ainsi la surproduction et l’accumulation d’inventaire.
- Amélioration continue : L’entreprise doit toujours chercher à s’améliorer pour assurer sa pérennité et son succès face à la concurrence.
Les outils clés facilitant la démarche Lean
Diverses techniques et outils sont employés dans le cadre du Lean Manufacturing pour aider les entreprises à mener efficacement leur transformation :
Jidoka : Automatisation avec une touche humaine
Le concept de Jidoka vise à intégrer la qualité dans les processus de production dès le départ. Il permet aux opérateurs de machines d’intervenir rapidement en cas de problèmes détectés, d’en identifier la cause racine et d’empêcher la production de pièces défectueuses. Cela contribue à minimiser les pertes liées à la non-qualité et à améliorer la performance des activités industrielles.
Kaizen : Amélioration continue et progressive
Le Kaizen se traduit littéralement par « changement positif » et fait référence à la mise en place d’un environnement favorisant l’amélioration permanente et à l’implication active de tous les collaborateurs. Il peut prendre différentes formes, telles que des ateliers résolvant des problèmes spécifiques, ou des initiatives individuelles visant à optimiser les postes de travail et les pratiques professionnelles. L’objectif est de créer une dynamique d’évolution constante et atteindre un état d’excellence opérationnelle.
5S : Un espace de travail organisé et optimisé
Le système 5S, originaire du Japon, est un ensemble de cinq actions permettant l’organisation et la gestion optimale des espaces de travail :
- Seiri (débarrasser) : Trier et ne conserver que le matériel indispensable pour réaliser les tâches quotidiennes.
- Seiton (ordonner) : Organiser l’espace dans un souci d’efficacité et de rationalisation.
- Seiso (nettoyer) : Assurer un environnement propre et sain favorisant concentration et performance.
- Seiketsu (standardiser) : Mettre en place des règles communes et des procédures garantissant l’uniformisation des pratiques.
- Shitsuke (maintenir et progresser) : Former et sensibiliser les collaborateurs à l’amélioration continue et au respect des standards établis.
Les bénéfices notables d’une démarche Lean
Lorsqu’elle est adoptée et appliquée avec efficacité, la méthode Lean Manufacturing permet aux entreprises d’obtenir divers avantages compétitifs :
- Rentabilité accrue : La réduction des gaspillages au sein des processus industriels contribue à une meilleure maîtrise des coûts et, par conséquent, à une augmentation de la marge bénéficiaire.
- Minimisation des délais : La réduction du temps de production permet de répondre plus rapidement aux besoins clients et d’améliorer la réactivité globale de l’entreprise.
- Qualité irréprochable : L’intégration d’une culture qualité forte au sein de l’organisation diminue le risque de défauts et renforce la satisfaction client.
- ‘Engagement et motivation des collaborateurs : Les initiatives Lean favorisent généralement un meilleur climat social en sollicitant les compétences et les idées de chacun dans le processus d’amélioration continue.
Les entreprises ayant réussi à mettre en œuvre le Lean Manufacturing ont ainsi pu constater des gains significatifs en termes de qualité, productivité et rentabilité. Néanmoins, pour assurer un déploiement efficace de cette méthode, il est indispensable d’adopter une approche sur-mesure, intégrant l’ensemble des parties prenantes de l’entreprise et s’appuyant sur des objectifs clairs et partagés.